Renishaw NC4+ Blue Expands Range, Improves On-Machine Measurement Repeatability
Blue laser technology has a shorter wavelength which is said to result in optimized laser beam geometry, enabling the measurement of very small tools.
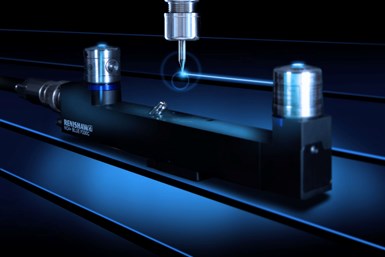
NC4+ Blue F230 noncontact tool setter. Photo Credit: Renishaw
Renishaw’s NC4+ Blue noncontact tool setter has been updated to feature an ultracompact design and is now available in four sizes, with operating gaps ranging from 55 mm to 240 mm. Measurement repeatability has also been improved across the range, now down to ±0.5 microns on smaller separations.
The company says it offers improved machining accuracy, featuring blue laser technology and improved optics. The tool setter is said to deliver significant improvements in tool measurement accuracy.
The blue laser technology has a short wavelength that enables the measurement of very small tools, while minimizing tool-to-tool measurement errors. The NC4+ Blue systems use Renishaw’s noncontact tool setting software package.
Auto-optimization technology within the software automatically adjusts the movement of the tool in and out of the beam to minimize any wasted movement and, therefore, cycle time. It features a dual measurement mode where the tool is measured as it exits the laser beam and an advanced tool cleaning option to help ensure the tool is free from debris and coolant during measurement. Further enhancements to tool runout and profile measurement cycles are said to deliver increased functionality and reliability to advanced users.
The NC4+ Blue uses MicroHole and PassiveSeal optical protection technologies. The MicroHole technology is said to ensure the optics are protected from contamination during measurement by delivering a continuous stream of compressed air through a very small, precise laser-drilled hole in the transmitter and receiver heads. The PassiveSeal system provides an additional layer of protection, automatically shielding the optics from contamination in the event of air supply failure. It uses a simple pneumatic installation that minimizes any need for maintenance.
Related Content
-
Shop Finds Value in Simple CMM Programming
Icon-driven programming enables all shopfloor personnel to perform CMM inspection, not just those in the quality department.
-
Precision Machining Technology Review December 2022: Measurement
Production Machining’s December measurement showcase includes some of the latest technology from Haimer, Hamar, Sunnen, OGP, Marposs and Zeiss.
-
Addressing Machining’s Necessary Evil
Many view quality control as such, but integrating new measurement technologies and approaches can ultimately minimize QC’s impact on throughput and a company’s bottom line.