An Additive Solution for Copper Inductors and Heat Exchangers
Solution delivering more capable inductors debuts as standard product for other fine-detail copper needs.
Additive manufacturing is a broad category. It consists of many different 3D printing processes, offering applications in practically every sector of part production. However, the advance of AM is, in part, leading to solutions that are increasingly specific — tailored to focused needs additive can serve.
Precision copper components is the latest application additive manufacturing technology provider EOS is serving in this way. Its AMCM M 290-2 1 kW laser powder bed fusion system, seen in the company’s booth #432302, is designed to 3D print copper components with fine geometric precision. Target applications are copper inductors and heat exchangers.
The “AMCM” in the machine’s name stands for Advanced Manufacturing Custom Machines, a part of the EOS team focused on engineering custom systems for manufacturers in need of tailored additive solutions. The company that applied this (formerly) custom solution was able to realize an optimized inductor design, made additively, that achieved a 60% manufacturing cost reduction and 50% power savings in operation compared to a conventionally made inductor design. The AM solution for precision copper parts is now available as a standard machine, making its debut at IMTS.
The company says part of what makes this machine different from other laser powder bed machines is the combination of a large build envelop with a fine 85-micron spot size for the system’s two-beam 1-kW fiber laser system. Combined with the right process parameters, the new machine produces copper forms that realize 100% electrical conductivity per the International Annealed Copper Standard.
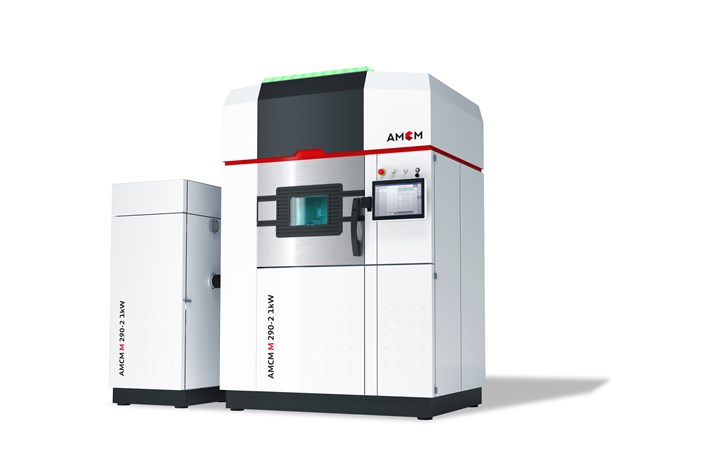
The AMCM M 290-2 1 kW is a successful custom product now available as a standard machine.
RELATED CONTENT
-
Questions about Precision Machining? Ask Index
At this IMTS, Index Corp. is challenging show visitors to Ask Index key questions, the answers to which can help them ready their businesses for the next five years or more.
-
Starrett's Multisensor Vision System Provides Large Field of View
IMTS 2022: The AVR-FOV 0.14X multisensor vision system is designed to provide accurate, efficient measurements fora wide range of parts.
-
See Chip Control and Chipless Cutting at Marubeni Citizen-Cincom
Visit Marubeni Citizen Cincom’s booth to see how the new Low Frequency Vibration (LFV) cutting technology deals with the problem of chip accumulation.