How Advancements in CNC Multi-Spindles Can Put You Ahead of Current Trends
Growing economic and labor pressures are making CNC multi-spindle turn/mill technology more viable than ever. This real-world comparison to a single-spindle lathe shows how.
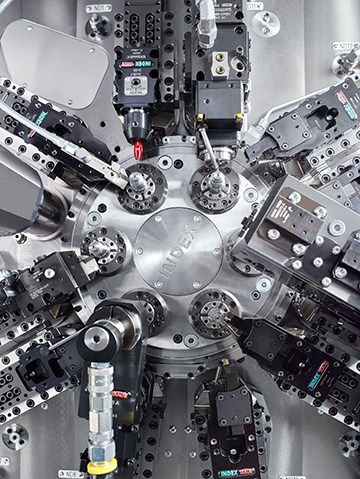
Amidst global events that have shaken the world’s economies, American manufacturers face a range of challenges both new and familiar. The actions taken to overcome these hurdles will vary from company to company. For those who produce medium-to-large lots of parts 2" or smaller in diameter, the most impactful solution may lie in the adoption of advanced CNC multi-spindle lathes.
You’re Not Alone
It’s no secret that manufacturers have a lot to deal with.
The skilled labor shortage has been a concern for most of the lives of those working in the industry today. The past two years’ dual waves of early retirements and mid-life career changes have accelerated the trend, making it harder for companies to recruit and maintain the teams they need to grow.
Sporadic supply chain issues have arrived in waves as countries vital to the world economy have instituted lockdowns in efforts to protect their populations. Each has added to the others, rippling out to create a state of persistent disruption that has been further aggravated by war in Europe.
And last but not least, inflation has shaken multiple nations, driven by two years of pent-up savings and demand outpacing supply. This introduces cost-related stresses to every manufacturer, as customers resist price increases even as suppliers demand them.
The good news is that you’re not alone. Each of your competitors is facing down the same host of issues. By identifying and implementing strategies to adapt, you can carve out an advantage that will lead to long-term growth.
The State of the CNC Multi-Spindle
So how can CNC multi-spindles help manufacturers gain an edge? To answer that, one needs to first understand how this machine technology has evolved over the past decade.
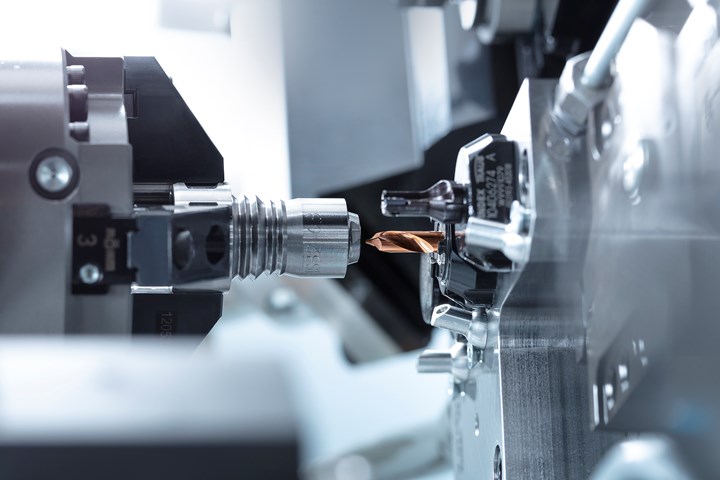
By executing different workpiece operations simultaneously on multiple spindles, machine cycle times can be dramtically reduced.
Historically, multi-spindles were sometimes viewed as rather inflexible solutions. If you had steady demand for a very high quantity of a fairly simple part or family of highly similar simple parts, you might consider a multi-spindle. It could take a significant amount of time to iron out the process and get it set up, but once it was running, the machine could produce parts dramatically faster than competing technologies.
Today’s CNC multi-spindles offer that same advantage in speed, but with much more flexibility.
WATCH: Advanced Engineering in Action
At INDEX, for example, all current generation multi-spindles incorporate a modular system. Whether looking at a 6-spindle or 8-spindle machine, each spindle is served by two tool slides that can quickly and easily be swapped out. Slides can hold static or live tools, and can be equipped with C and Y axes, in addition to the standard X and Z axes. This flexible, modular approach opens up a lot of possibilities.
Current gen multi-spindles can machine far more complex parts than used to be possible. In addition to the typical range of turning, milling and drilling operations, the machines can perform more specialized processes, such as off-center drilling, threading, contouring, hobbing and polygonal turning. Additionally, machines can be equipped with either one or two backworking attachments, allowing highly complex parts to be fully cut with no need for secondary processing.
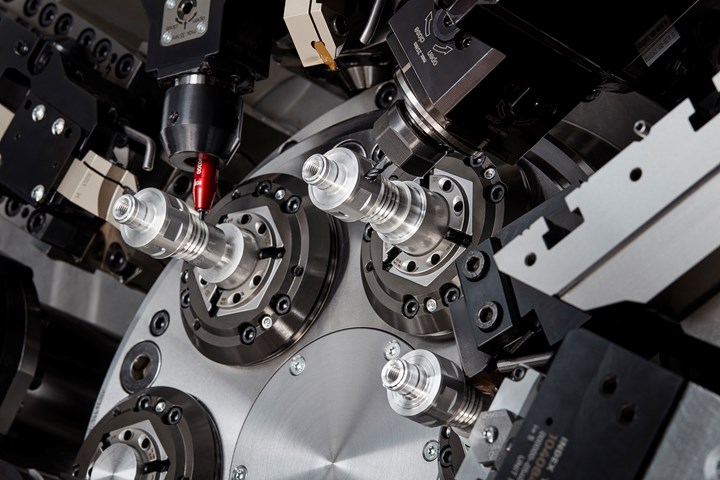
Modern multi-spindle technology can perform almost any turning and milling task, all under CNC control.
The modular approach also simplifies changeovers. INDEX uses a patented W-serration locating system that allows users to simply loosen a holding screw and remove the current slide, then position a new slide and tighten its holding screw. The W-serration system automatically ensures proper positioning, with µm-accurate alignment. With older multi-spindles, changing over the machine meant suffering significant downtime. The new system allows the presetting of tooling off of the machine, followed by incredibly quick changeovers. This lets manufacturers economically run relatively smaller lot sizes on the machine, bringing the benefits of the technology to a far wider range of parts.
Lastly, advancements in software have greatly simplified the programming of a CNC multi-spindle. In reality, the difficulty of programming these machines was overstated in the past. After all, essentially a multi-spindle user is just programming either six or eight individual lathes, with much of the complexity stemming from the need to equalize processing time as much as possible across the spindles. But with software like INDEX’s Virtual Machine, creating and optimizing part programs has become incredibly efficient.
In short, the evolution of multi-spindle technology has made it applicable to a far wider range of parts and applications. Many shops that would not have been able to benefit from a multi-spindle at the turn of the century could achieve significant gains by adopting the technology as it exists today. Let’s take a quick look at an example from one who has.
Real World Impact
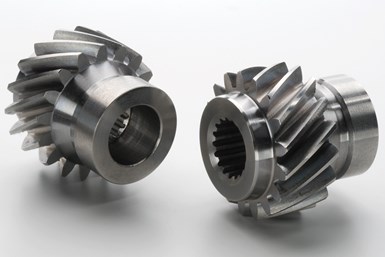
Producing this helical pinion gear on a multi-spindle generates nearly 12 times the profit compared to a single spindle lathe.
Used in differential transmissions for the e-mobility segment, this helical gear is machined from 15MnCrS5 steel alloy. It measures 0.79" (20 mm) in diameter with a length of 0.98" (25 mm). On an INDEX MS24-6 multi-spindle, the cycle time is just 11 seconds. On a single-spindle lathe, it was 38 seconds.
For this comparison, let’s assume an order for 20,000 pieces at an even price of $1.00 per piece.
To start our comparison, we look at how long it would take the two machines in question to complete the job. We’ll assume a 5-day work week with the machines operating 20 hours per day.
Single-Spindle Lathe |
MS24-6 Multi-Spindle |
|
Total quantity |
20,000 |
20,000 |
Cycle time (seconds) |
38 |
11 |
Hours to complete job |
211.1 |
61.1 |
Days to complete job |
10.6 |
3.1 |
Next, we’ll calculate the machine portion of the cost for both scenarios.
Single-Spindle Lathe |
MS24-6 Multi-Spindle |
|
Approximate price |
$500,000 |
$1,785,000 |
Finance period (months) |
84 |
84 |
Interest rate |
5.75% |
5.75% |
Monthly payment |
$7,245 |
$25,863 |
Annual total of monthly payments |
$86,934 |
$310,354 |
% of year allocated to job (days to complete job / 250) |
4.2% |
1.2% |
Machine portion of job cost |
$3,671 |
$3,793 |
Finally, we need to add a shop rate to account for overhead beyond the machine. This number can vary quite a bit, but $60 is an average rate. By plugging this in, we can determine the profitability of the job under both machines.
Single-Spindle Lathe |
MS24-6 Multi-Spindle |
|
Revenue from job |
$20,000 |
$20,000 |
Machine portion of job cost |
$3,671 |
$3,793 |
Overhead portion of job cost ($60 x hours to complete job) |
$12,667 |
$3,667 |
Net profit for job |
$3,663 |
$12,540 |
And just to drive the point home, let’s take a quick look at what the profitability of each machine looks like over the course of the year. For simplicity’s sake, we’ll assume that the shop can win a steady supply of work with ratios that are identical to the above example.
Single-Spindle Lathe |
MS24-6 Multi-Spindle |
|
Annual number of jobs (250 / days to complete job) |
23.7 |
81.8 |
Net profit per job |
$3,663 |
$12,540 |
Annualized profit for machine |
$86,750 |
$1,026,009 |
Put simply, the power of productivity is so impactful on profits that even though the multi-spindle costs more than 3x the single-spindle machine, it generates nearly 12x the profit. In fact, the effect is so dramatic that even if you dropped the cost of the single-spindle lathe to $0, the multi-spindle would still be 490% more profitable to operate.
Are Multi-Spindles Right for You?
As demonstrated in the above example, for the right type of parts, there is simply no faster, more cost efficient method of production. The advantage becomes even greater in the current environment.
By significantly reducing per-part costs, a CNC multi-spindle can immediately reduce the stress of pricing pressures. This provides more flexibility to negotiate, both with vendors and customers.
For shops having difficulty finding skilled operators, multi-spindles offer a path to growth within the bounds of your current team. Generally, a multi-spindle requires no more operator intervention than any other type of machine, yet will produce anywhere from 400% to 600% of the output. If labor is constraining your ability to win new work, a multi-spindle can be liberating.
The same holds true for shops butting up against the limitations of their facility size. When a company is growing, but also approaching maximum usage of its facility’s floorspace, something has to change. Many times, a company will opt to purchase a new building or expand an existing one. Conversely, simply replacing several more traditional machines with CNC multi-spindles can grow capacity within the existing footprint, offering the potential for growth with a smaller, more efficient investment.
While current market trends may seem daunting, every challenge provides an opportunity. Over the past two years, INDEX has helped many North American manufacturers accurately evaluate the impact multi-spindle technology would have on their unique operations. If you’d like expert assistance in conducting such an evaluation for your own company, please contact INDEX at sales@index-usa.com.