Slings — Critical Infrastructure in Your Shop
Safe sling use is critical for a safe work environment.
#pmpa
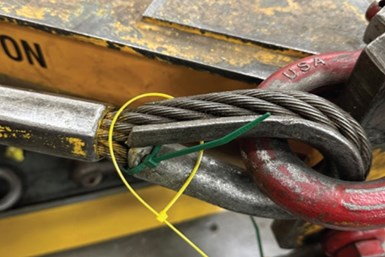
Color-coded cable ties indicate inspection status.
Photo Credit: PMPA
Synthetic web slings, cable slings and alloy chain slings carry most, if not all, of the raw materials over the machines and equipment in our shops. Slings may also be used to move other items and are generally used with an overhead crane. It would not be uncommon for lifts of a ton or more to be carried by slings — 2,000-pound bundles of bar stock for machining are common. A sling failing while carrying that much would cause catastrophic damage to the machines and equipment below. And if the bars rebound, they could strike employees causing injury or death, even though they were not directly below the lift.
Here is a review of OSHA guidance and best practices that I have observed to ensure safe usage of synthetic web slings, which are the most frequently encountered type of slings encountered in our shops.
Featured Content
Identification
OSHA requires that new slings be marked by the manufacturer to show the rated load for each type of hitch and the type of material used. Additional markings may include the manufacturer’s stock number or code as well as the name and trademark of the manufacturer.
Best practice: to facilitate tracking for inspection purposes, I have seen shops assign a unique sling identifier. Identifiers can be by date purchased and a shop-created sling number, or by department or area used and sling number.
Inspections
Inspections must be performed daily before use, but also at defined intervals based on service and duty.
According to OSHA’s guidance document, periodic inspections must be made at intervals no greater than 12 months. Normal service use would merit an annual periodic inspection. Monthly or quarterly additional inspection is indicated where slings are subject to severe service use, and for slings used infrequently or for special service, as recommended by a qualified person.
The point of an inspection is to ensure that damaged or defective slings are immediately removed from service to prevent accident or injury. The inspection must be performed by a competent or qualified person. Under the 1926 construction standard, a competent person is one “who is capable of identifying existing and predictable hazards in the surroundings or working conditions which are unsanitary, hazardous, or dangerous to employees, and who has authorization to take prompt corrective measures to eliminate them” (OSHA link: bit.ly/PMPA-PM0923a).
The general industry (1910) standard defines a qualified person as one who “…by extensive knowledge, training, and experience, has successfully demonstrated the ability to solve or resolve problems relating to the subject matter and work” (OSHA link: bit.ly/PMPA-PM0923b).
No one should be using slings until trained to recognize existing hazards which would be dangerous and has been authorized to take prompt corrective action. Have you trained all of your employees to recognize hazards and dangers and authorized them to take immediate necessary action?
Inspection Criteria
So what are some conditions that would merit removing the sling from service immediately? Most frequently encountered in our shops would likely be slings showing holes, tears, cuts, snags, excessive abrasive wear, evidence of chemical or thermal burns, melting or charring on any part of the sling. The presence of knots in any part of the sling are also cause for immediate removal from service, as it is evidence of discoloration and brittle areas, or other conditions that “cause doubt” as to the continued use of the sling. Missing identification is also noted as grounds for removal from service. This list is not complete, but it covers the most likely and frequently observed conditions in small manufacturing shops.
Inspection Best Practices
What has remained out of reach of most shops has been a way to see if the periodic inspection of a web sling has been performed. It’s unwieldy to look up inspection records on paper or even online, so it is unlikely to be followed. However, I was impressed with the following best practice encountered on our PMPA Mastery Program Tour visit to Mazak in Florence, Kentucky. At Mazak, the periodic inspection status of every lifting device (web slings as well as cables and alloy chains) was displayed by the use of a color-coded nylon cable tie secured around one side of the “eye” or the sling fitting. The color code showed the most recent additional inspection period status — if the proper color for the latest period was not attached, the employee could see this instantly. The cable tie provides immediate visual inspection status while providing no hazard to the sling or its use.
Slings provide critical operational support for our shops. They also hold the potential for great damage and personal injury should they fail. Follow the guidance above to keep your operations safe. Use color coded cable ties as a visual management indicator of sling inspection status — a best practice for shop safety, operations and visual management.
About the Author
Miles Free III
Miles Free III is the PMPA Director of Industry Affairs with over 50 years of experience in the areas of manufacturing, quality and steelmaking. Miles’ podcast is at pmpa.org/podcast. Email: mfree@pmpa.org — Website: pmpa.org.
RELATED CONTENT
-
Subscribe to PMPA Podcasts
"Speaking of Precision" is a podcast from Industry expert Miles Free III, in which he talks about precision machining. All episodes may be found on major platforms.
-
Ventilator Crisis — Clippard Delivers for Ford
Clippard Instrument Laboratory Inc. in Cincinnati, Ohio, harnessed their talent, experience, capabilities and PMPA network to deliver 50,000 sets of ventilator parts to Ford Motor Company.
-
Quality — A Better Definition for Manufacturing
Quality is a critical factor in manufacturing. Has the definition changed over the years?