Mitsubishi LoadMate Robotic Cell Streamlines Parts Loading, Unloading
Appears in Print as: 'Robotic Cell Streamlines Parts Loading, Unloading'
Machine Tending Robotic Cell features portability, easy setup and programming, high performance and safety layout for both job shops and larger scale production environments.
Edited by Angela Osborne
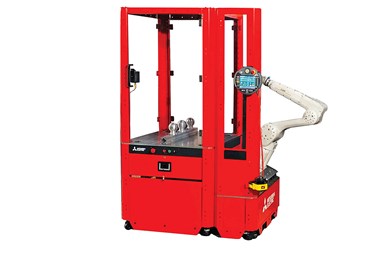
LoadMate Plus Machine Tending Robotic Cell
The LoadMate Plus Machine Tending Robotic Cell from Absolute Machine Tools’ partner Mitsubishi Electric Automation streamlines part loading, unloading and palletizing in low-to-high volume applications. It features portability, easy setup and programming, high performance, and a safety-first design that make it appropriate for both job shops and larger scale production environments, the company says.
Mitsubishi and Absolute jointly designed the plug-and-play cell. It consists of a Mitsubishi industrial robot, wheeled stainless steel base, clear polycarbonate cell enclosure featuring a safety door with an interlock switch, and a side table extension. The cell accommodates Mitsubishi 6-axis RV-series robots, ranging in load capacity from 7 to 20 kg and reach up to 1,388 mm. Integrating the robot cell with a CNC machine is a one-step process using a single Ethernet cable, Mitsubishi’s Direct Robot Control function and the Mitsubishi M8 series control. The LoadMate Plus can also interface with other control types via remote I/O connectivity.
Built-in casters enable users to move the LoadMate cell from machine to machine. The cell enclosure is designed to handle heavy payloads and significant part momentum. Additional guarding and fencing may not be necessary when the cell is positioned correctly in tandem or in close proximity to the CNC machine. Depending on the application, the cell can be secured in position using built-in ratchet pads or an optional floor-mount latching system.
RELATED CONTENT
-
Making Waves with Lathe Automation
After years of relying on an extensive machining cell for part production, this marine equipment manufacturer has now reduced part handling and improved quality through use of single-setup lathes and automated loading and unloading.
-
Simplifying Machine Load/Unload Automation
Today, lower part volumes and frequent change-over are changing the offerings of some automation integrators. Standard, off-the-shelf components are being engineered to work together in a large variety of applications and, in some cases, are even portable so they can be moved from machine tool to machine tool.
-
What Is The Best Bar Feed System For Production Turning?
Selecting the right bar feeder can be one of the most important decisions a shop can make. Bar feed systems help improve productivity, throughput and quality, but in order to achieve the most benefit from them it is essential that a bar feed system be matched to the particular needs of the turning operation.