SMW Autoblok Twin Vise Stability Enables Higher Cutting Speeds, Feed Rates
Appears in Print as: 'Twin Vise Stability Enables Higher Cutting Speeds, Feed Rates'
The PTP/PTH compact twin vises are said to feature a high failsafe clamping force up to 60 kN and case-hardened components for high precision and long life.
Edited by Angela Osborne
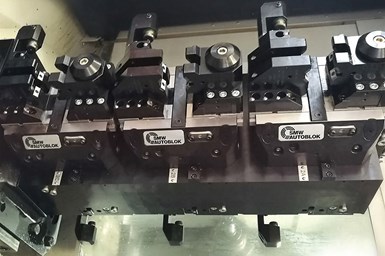
SMW Autoblok’s fully automated compact PTP/PTH Series Twin Vise. Photo Credit: SMW Autoblok
SMW Autoblok’s fully automated compact PTP/PTH Series Twin Vise is designed to provide pneumatic and hydraulic clamping force with a standard jaw stroke, long stroke or one fixed jaw stroke control.
The company says the vise is well suited for automation. The self-centering PTP pneumatic and PTH hydraulic Twin Vises can be a seamless solution for tombstone and storage problems as well as 4- and 5-axis multipallet machining centers with or without robot loading.
The compact vises are said to feature a high failsafe clamping force up to 60 kN and case-hardened components for high precision and long life. Effective for both OD and ID clamping, the spring-loaded twin vises can be used with industry standard or engineered top jaws, the company says.
Optional SinterGrip clamping inserts are available, which provide no dovetailing and have 3.5-mm clamping depth (versus 30-mm standard). Adding these inserts is said to reduce the waste of expensive raw materials and minimize deformation.
According to the company, a series of solid carbide-serrated inserts grip the workpiece securely so that vibration is virtually nonexistent. This stability is said to enable higher cutting speed and feed rates, which can translate into more metal removed in less machining time.
All modules are Proofline sealed to protect against corrosion and feature a built-in air cleaning function to ensure the clamping system’s support surface remains clean and free of chips during changeover or automation. This feature is said to reduce maintenance and production time, and provides a repeat accuracy of up to 0.01 mm. Sizes include 100, 120, 160 and 200 mm.
RELATED CONTENT
-
Collets Vs. Chucks
Find the definition, types and advantages of both CNC collets and chucks for workholding as well as the best applications for each, in this article.
-
5 Process Security Tips for Parting Off
Here are five rules of thumb from Scott Lewis, a product and application specialist at Sandvik Coromant, to optimize the parting off process, and as a result, maximize tool and insert life.
-
4 Strategies for Managing Chip Control
Having strategies in place for managing chips is an important part of protecting the production process, from tool life to product quality.