Somex Offers Direct Integration of Deep-Hole Drilling Module
Appears in Print as: 'Deep-Hole Drilling Module Offers Direct Integration'
For deep hole drilling applications larger than 18-mm diameter, Somex offers optional Max machining units with drilling systems from BTA or Ejektor lines.
Edited by Angela Osborne
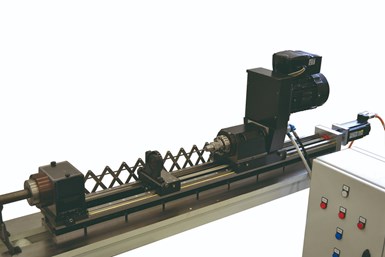
Due to its modular component concept, Somex says it can provide customized, turnkey, small and economical deep-hole drilling machines.
Somex, a member of the Suhner Group, offers custom deep-hole drilling capable of drilling up to 12-mm diameter and as deep as 100X the diameter. The modules can be integrated directly into transfer machines, special-purpose machines or conventional machines such as turning machines.
In addition to standard Max machining units, the company also offers peripheral components. Due to its modular component concept, Somex says it can provide customized, turnkey, small and economical deep-hole drilling machines.
The deep-hole drilling process typically requires either a pilot drill 1.5X the diameter or a drill guide bushing, which is then followed by the deep-hole drilling process. The Somex design concept combines the guide bushing with a chip basket, enabling both items to travel in unison. The movement of the guide bushing is air-driven, which is said to help provide a much closer contact to the part while preventing the escape of the coolant medium.
For longer deep-hole drilling applications, it may be necessary to integrate a support bushing to stabilize the deep-hole drilling tool. According to the company, the degree of accuracy in a deep-hole drilling application measured in the deviation from the theoretical part center line is greatly enhanced by a slow part rotation in a counterclockwise direction.
For deep-hole drilling applications larger than 18-mm diameter, Somex offers optional Max machining units with drilling systems from BTA or Ejektor lines. In these applications, the coolant and chip management is accomplished through the spindle center. The emulsion is collected at the back end of the spindle, filtered and pressurized to reenter the coolant system. This solution is often used in high-volume precision parts manufacturing such as automotive and other industries, the company says.
RELATED CONTENT
-
Skiving Long, Slender Parts with Tight Tolerances
Here's a look at one of the oldest and most efficient methods of screw machine production for parts that are long and slender, with close-diameter tolerances and finishes, or parts that require truly spherical radii.
-
Tools and Technologies for Deep Hole Drilling
Understanding the challenges of deep hole drilling and knowing how to select and apply the appropriate tools will help a shop profit from this operation.
-
Making Micro Threads
Production of micro threads can be challenging, but using the most suitable tools for a given application can simplify the task.